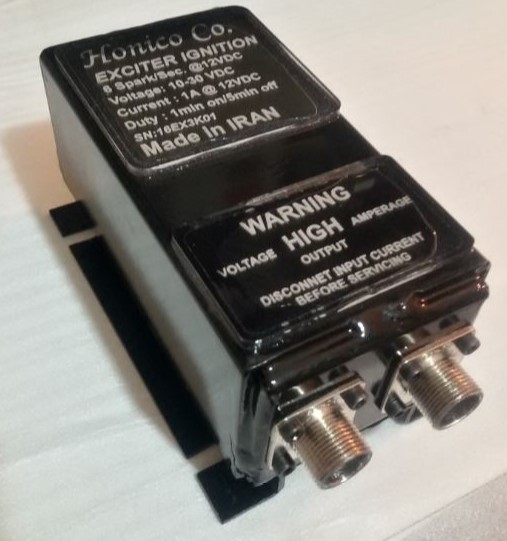
Turbine Ignition Systems: A Key Role in Safe and Fast Start-Up
In the turbine start-up process, the ignition system acts as the heart of combustion initiation. This system consists of three key components: the Exciter, the Ignition Cable, and the Igniter Plug. Working in full coordination, they ignite the fuel-air mixture in the initial phase, serving as the trigger for stable turbine operation.
1- Exciter: The Power Source for Ignition
Exciter (Ignition Unit) is a high-voltage generator that provides the energy required to create the ignition spark. In turbine systems, it must meet the following criteria:
-
High and stable output voltage, typically in the range of several thousand volts
-
Ability to generate repetitive pulses at appropriate frequencies
-
High resistance to heat, vibration, and harsh environmental conditions
In advanced designs such as Honico’s products, exciters are equipped with protective systems and precise control mechanisms to ensure safe and reliable ignition.
2- Ignition Cable: The Critical Connection Bridge
The ignition cable serves as the conduit between the exciter and the igniter. It must possess specific features:
-
Strong insulation against high voltage
-
High thermal resistance (up to 200°C or more)
-
Durable structure resistant to pressure, vibration, and corrosion
The design and quality of the cable have a direct impact on the reliable transfer of high voltage to the igniter. In industrial turbine systems, even minor leakage or voltage drop in the cable can lead to delays or failures during startup.
3- Igniter: The Final Spark
The igniter, or spark plug, is the final component in the ignition system that converts high voltage into an actual spark. Its design must:
-
Include electrodes resistant to wear and high temperatures
-
Ensure proper arc formation for reliable ignition
-
Offer long service life and easy replacement
Turbine igniters are typically made from durable materials such as nickel alloys, tungsten, or industrial ceramics, as they operate in extreme conditions with high airflow and fuel exposure.
The Importance of Component Coordination in Overall Performance
In Honico’s advanced systems, the seamless integration between the exciter, ignition cable, and igniter ensures that:
-
Turbine startup occurs without delay and with a high success rate.
-
Overall system safety is enhanced, preventing the risks of incomplete combustion.
-
The service life of critical components is extended, leading to reduced maintenance costs.
Applications and Target Industries
Honico’s turbine ignition systems are used across a variety of industries, including:
-
Gas and thermal power plants
-
Aerospace industry and aircraft turbine engines
-
Turbine testing equipment in industrial laboratories
-
Emergency power generation centers and turbine-based diesel generators
Conclusion
Though turbine ignition systems may appear simple, they play a critical role in initiating, securing, and maintaining the stable operation of turbines. Honico, leveraging technical expertise and engineering experience, has designed and manufactured these high-quality systems to ensure that industries can rely on a powerful and precise start every time.